Future-Ready Transformation
Supply Chain Transformation
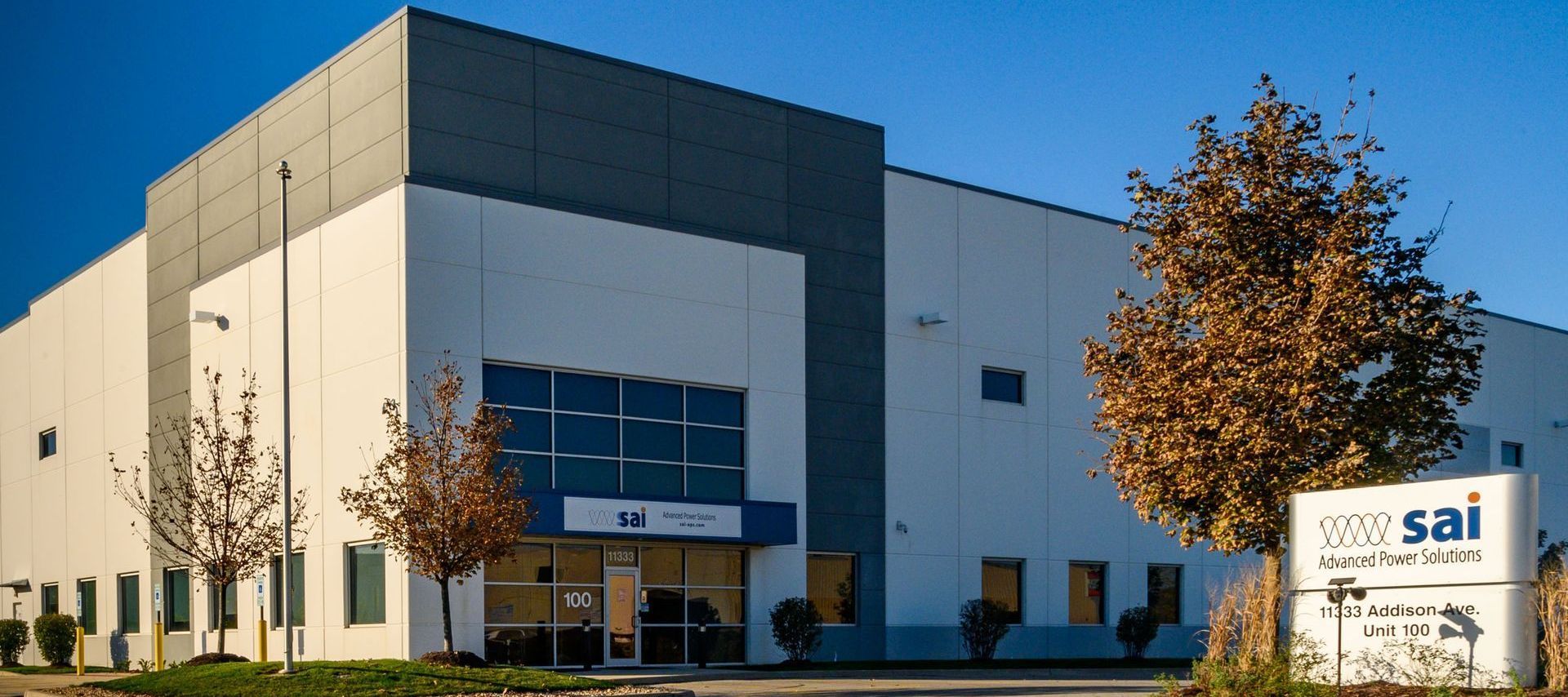
New world-class production center with distribution footprint expansion coming soon, 3X the size of our current production center.
Customer Focused Business Units
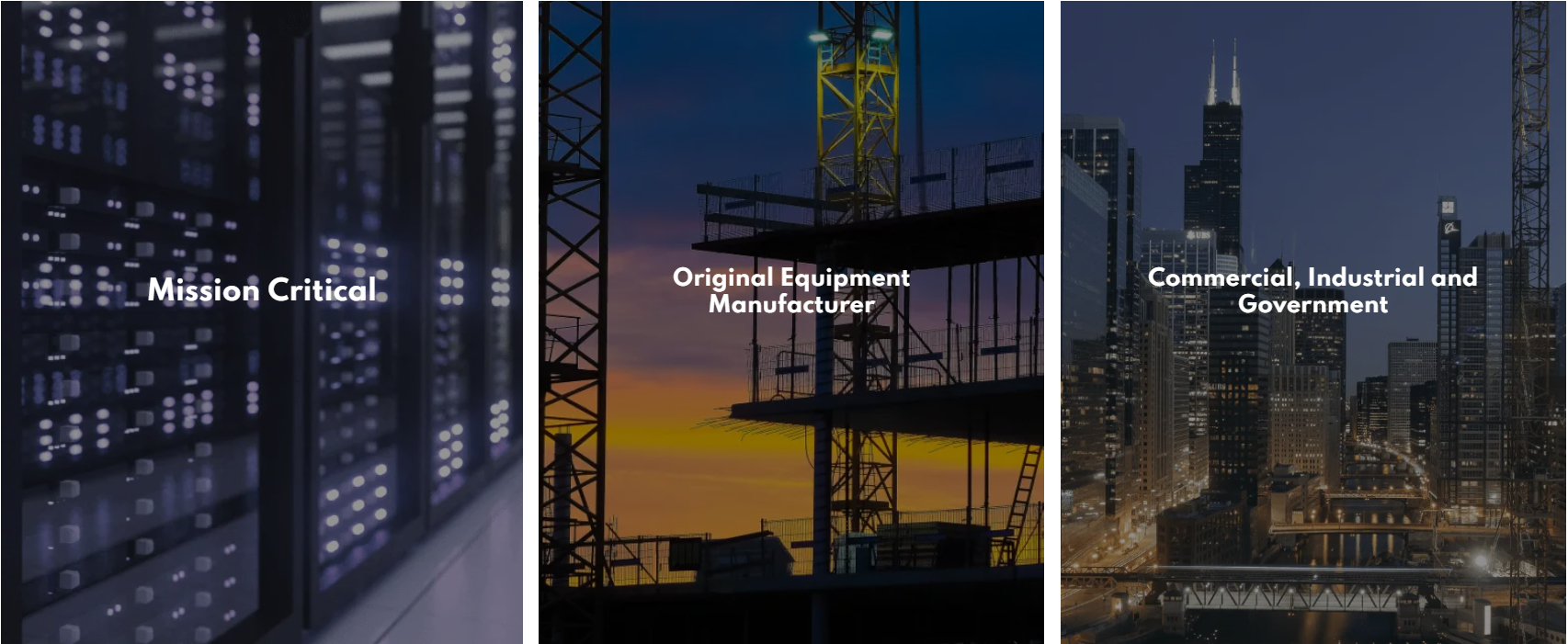
To better serve diverse market needs, organized to focus on market and customer segments namely OEM, Mission Critical and Commercial-Industrial-Government segments.
Breakthrough Innovations
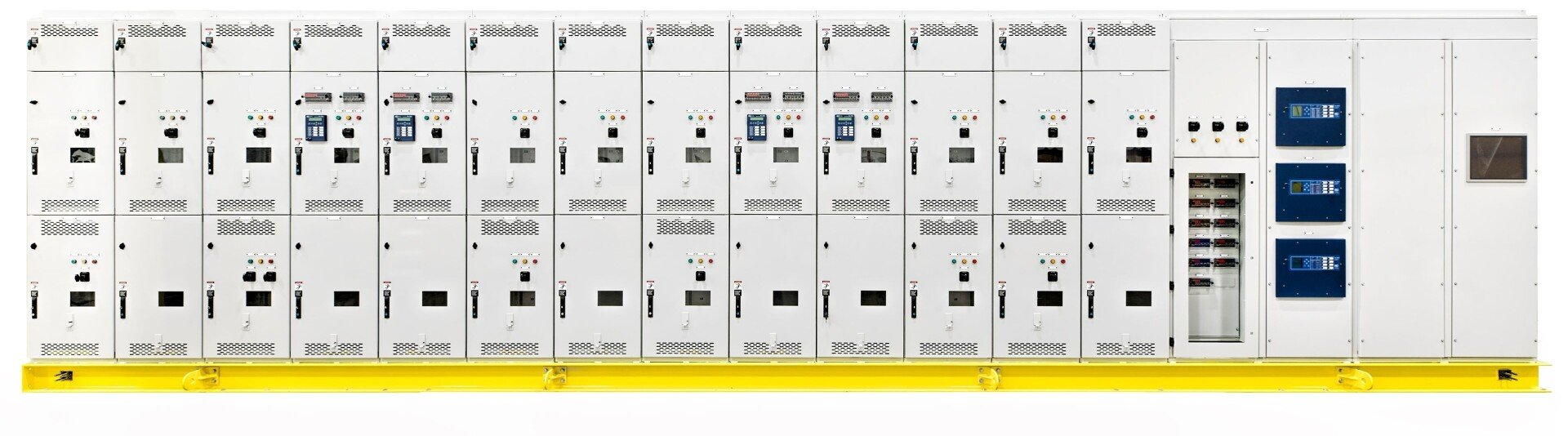
Innovative, patented, vast portfolio of products and services that meet customers’ needs and marketplace gaps – today and tomorrow.
Operations Transformation
Transformed operations with flexibility and capabilities to exceed the most discriminating and challenging solution portfolio, ranging from custom to low mix and high-volume solutions, giving SAI a significant competitive advantage in the marketplace.
Customer Success Teams
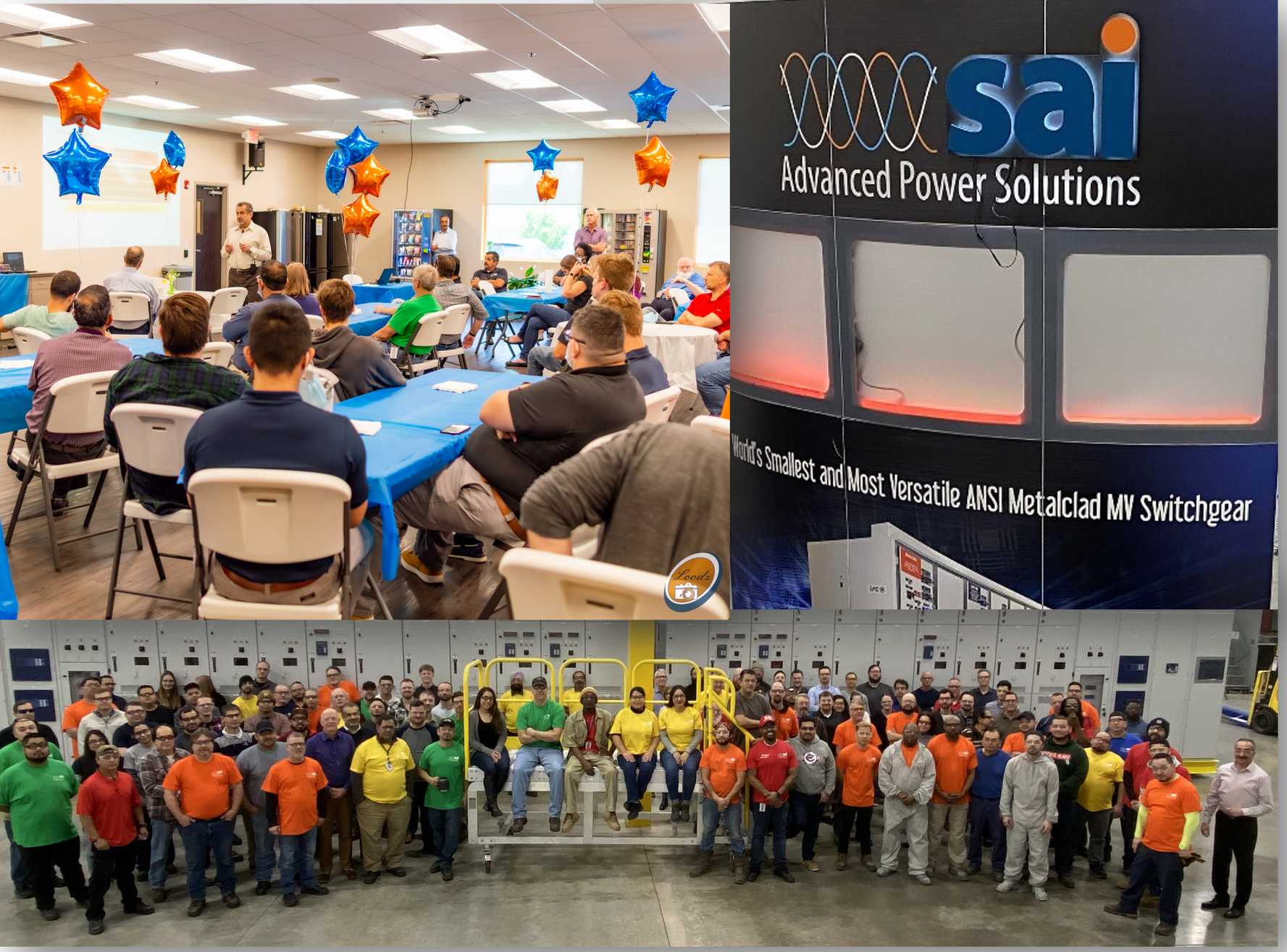
Everyone at SAI participates at Teaming for Customer Success (TCS) initiatives coupled with dedicated customer success specialists to exceed the expectations of our customers and partners with performance exceeding industry benchmarks.